India: Sourcing & Manufacturing
Costs, Production Timelines, Product Quality, Order Quantities, and Sourcing Strategies.
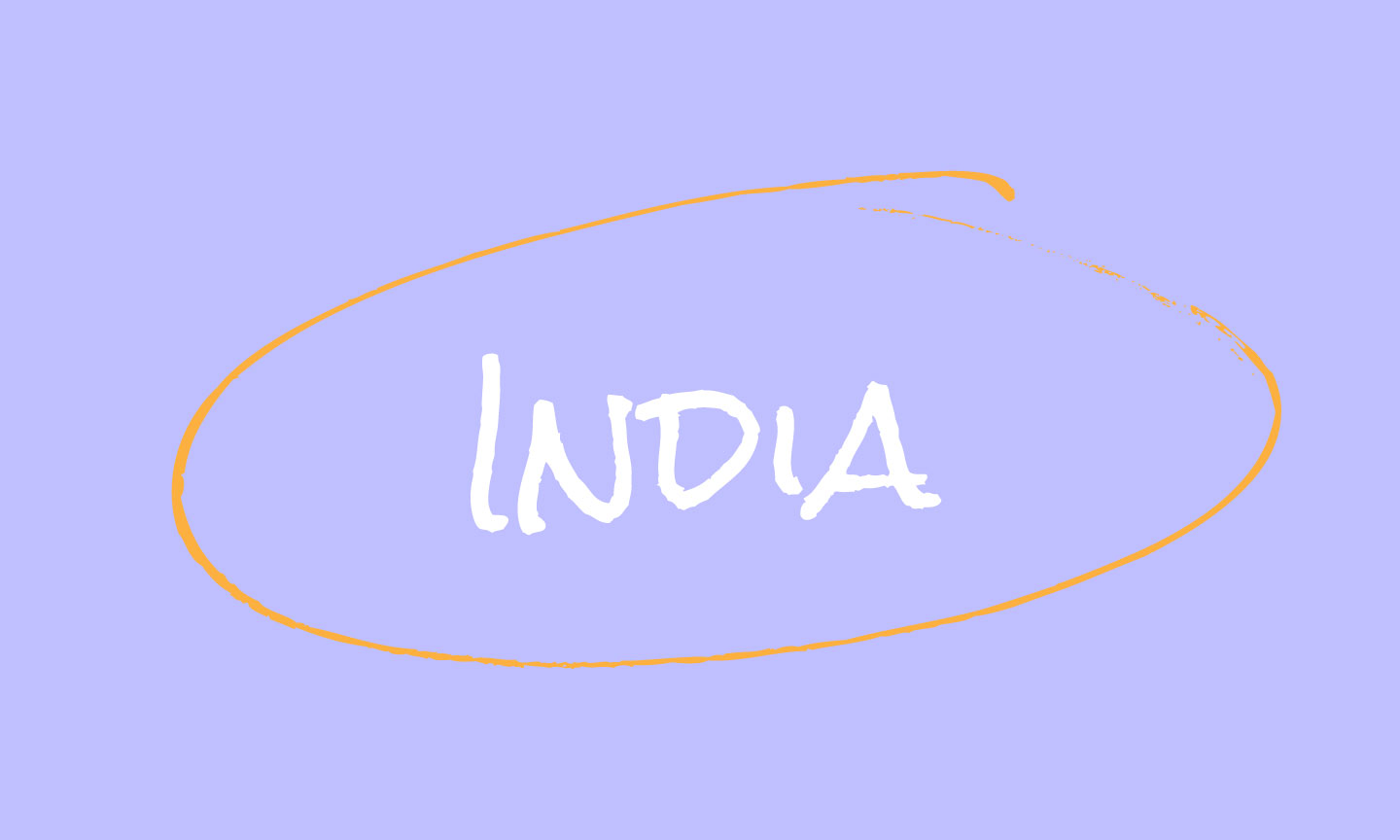
India Manufacturing Summary
Over the past decade, India has consistently ranked among the world’s fastest-growing major economies, achieving a ten-year compound annual real GDP growth rate of 8.2%, which is more than double the global average of approximately 3%. Roughly one quarter of this expansion has come from the manufacturing sector, which has strengthened across pharmaceuticals, jewelry and apparel.
A key advantage lies in India’s abundant domestic raw materials. As the world’s second-largest producer of both cotton and steel and the third-largest producer of specialty chemicals, India sources much of its raw-material needs locally. Although certain high-tech components are still imported, this strong base of domestic supply helps keep overall material costs low. Coupled with competitive labor rates, these factors make India an attractive destination for cost-sensitive production.
Communication is another often-overlooked benefit. English is widely spoken across India, so U.S. brands can interact directly with factory teams without language barriers. The country also boasts a large pool of engineers and skilled technicians, a capability that has supported rapid growth in consumer electronics manufacturing and encouraged companies such as Apple to expand iPhone assembly there.
However, quality consistency remains India’s biggest challenge, especially among small and medium-sized firms that offer the flexible order quantities favored by emerging brands. Manufacturing in India means it’s essential that you work with a third-party agent and/or quality-control service. Recognizing these issues, the Make in India initiative launched in 2014 included a zero-defect campaign to reinforce best practices, and while progress has been made, variability persists.
For those beginning their search, IndiaMART and TradeIndia are the two largest B2B marketplaces in the country. Together they list around seven million suppliers, searchable by product category and region, making them effective starting points for identifying potential manufacturing partners.
India Manufacturing: Advantages & Risks
Advantages:
- English-Speaking Workforce: Young, skilled workforce that speak English.
- Domestic Raw Material Sources: Strong raw materials base for soft goods making them less reliant on imports from China for a variety of materials keeping materials costs low.
- Significant Government-Backed Infrastructure and Manufacturing Incentives: Programs like Make in India and PLI schemes have driven the creation of modern industrial parks, dedicated freight corridors, and upgraded ports, steadily improving reliability and capacity.
-
Risks:
- Shipping Bottlenecks & Logistics Variability: While infrastructure has improved, persistent port congestion, intermittent power outages and limited road and rail connectivity can disrupt production schedules and extend lead times by several weeks. In addition, India’s geographic position adds extra days to sea freight transit to the United States.
- Quality Inconsistency & Skill Gaps: While top-tier plants excel, average supplier skill levels and automation maturity lag, often requiring intensive QC oversight and training to ensure reliable output.
-
Top 5 Product Specialties (in order)
- Electrical Machinery
- Consumer Electronics
- Pharmaceuticals
- Gems & Jewelry
- Apparel & Accessories
Key Data Points
- Avergae Costs
- Labor: Low
- Materials: Low
- Average Production Timelines: ~40-60 Days
- Typical Order Quantities (MOQ): ~1000-3000 Units
- Skilled Labor/ Quality Score: C
- Overall Ease of Business Score: C
-
Klugonyx Score: 5/10